Introduction
In the electric vehicle (EV) industry, the busbar is a critical component in the battery system, responsible for conducting electrical current between battery cells and modules. Choosing the right material for manufacturing busbars directly affects:
- Electrical conductivity
- System stability and safety
- Overall weight of the battery pack
- Production cost
Below are the five most commonly used materials for manufacturing EV busbars, along with their pros, cons, and typical applications.
1. Copper
Characteristics
- Extremely high electrical conductivity
- Excellent thermal conductivity and machinability
- Moderate oxidation resistance unless surface-coated
Advantages
- Delivers optimal current transmission efficiency
- Suitable for high-power battery systems
Disadvantages
- Heavy in weight
- Expensive
- Prone to oxidation if surface is not treated properly
Applications
- Battery systems in electric cars (4-wheel), fast-charging stations
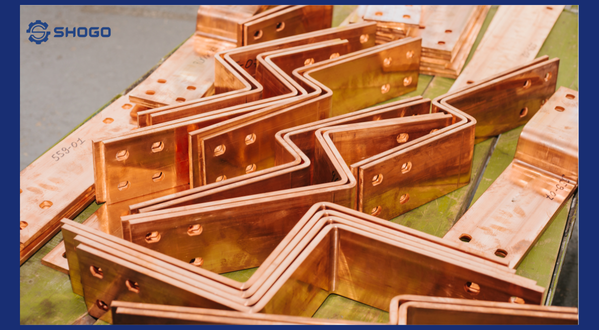
2. Aluminum
Characteristics
- 30–50% lighter than copper
- About 60% of copper’s electrical conductivity
- Low cost and easy to shape
Advantages
- Reduces vehicle weight
- Cost-effective solution for budget-sensitive projects
Disadvantages
- Requires larger cross-section to carry the same current
- Needs protective coating to prevent corrosion
Applications
- Electric scooters, entry-level EVs, cost-optimized designs
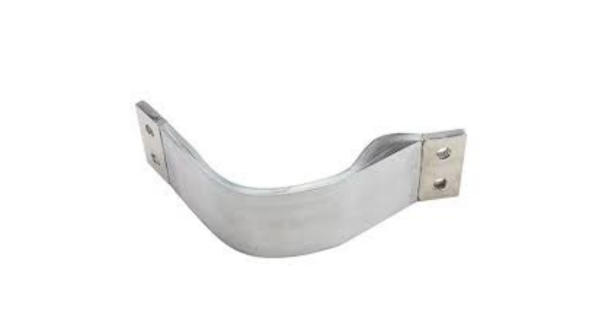
3. Nickel-Plated Copper
Characteristics
- Combines copper’s conductivity with nickel’s corrosion resistance
- Surface-plated for added durability
Advantages
- Extended lifespan
- Prevents galvanic corrosion when in contact with other materials
Disadvantages
- More expensive than plain copper
- Requires precise plating technology
Applications
- Premium EVs, batteries in high-humidity environments
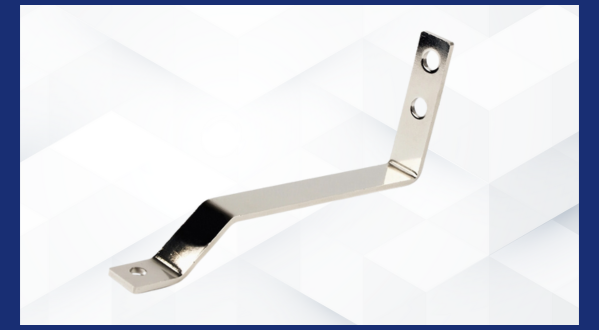
4. Pure Nickel
Characteristics
- Excellent resistance to oxidation and high temperatures
- Lower conductivity compared to copper or aluminum
Advantages
- Ideal for harsh environments
- No additional surface treatment required
Disadvantages
- Poor electrical conductivity
- High material cost
Applications
- Industrial EVs, military-grade or high-temperature applications
5. Flexible Busbar
Characteristics
- Typically made with copper or aluminum core, covered with flexible insulation (polyimide, epoxy, PET)
- Designed for compact and dynamic battery pack layouts
Advantages
- Easily bendable, ideal for complex designs
- Excellent electrical insulation and safety
Disadvantages
- More expensive due to insulation and lamination processes
- Requires strict quality control of insulation layers
Applications
- Electric motorcycles, drones, robots, flexible battery modules
Material Comparison Table
Material | Electrical Conductivity | Weight | Corrosion Resistance | Cost | Typical Applications |
---|---|---|---|---|---|
Copper | Very High | Heavy | Moderate | High | High-performance EVs, fast-charging systems |
Aluminum | Moderate | Very Light | Low | Low | Lightweight EVs, scooters, low-cost EVs |
Nickel-Plated Copper | Very High | Heavy | High | High | Premium EVs, humid environments |
Pure Nickel | Low | Heavy | Very High | Very High | Harsh conditions, military or industrial EVs |
Flexible Busbar | High | Light | High | High | Compact, modular EV battery designs |
Conclusion
Choosing the right busbar material impacts not only the manufacturing cost but also the performance, safety, and durability of electric vehicles. Each material offers distinct benefits and is best suited for specific applications.
Recommendations for EV Manufacturers and Startups
- For 2-wheelers or compact EVs: consider aluminum or flexible busbars
- For high-performance EVs or fast charging: prioritize copper or nickel-plated copper
- For extreme conditions: explore pure nickel or specialty alloys
Contact us today to get a technical consultation on the best busbar material for your EV project, along with free samples and datasheets.