1. Introduction
Busbar, also known as busbar, is an indispensable component in electrical systems. They play the role of transmitting electric current from the source to the consuming devices. Busbar is usually made from good conductive materials such as copper or aluminum.
However, during operation, busbar often faces many environmental factors, leading to corrosion, seriously affecting the efficiency and life of the electrical system.
2. Causes of busbar corrosion
Busbar corrosion is the process of metal being oxidized or reacting chemically with the surrounding environment, leading to surface decomposition.
The main causes of busbar corrosion include:
- Physical factors: High temperature, high humidity, ultraviolet radiation increase the rate of oxidation reactions, accelerating the corrosion process.
- Chemical factors: The presence of electrolytes (salts, acids, alkalis) in the air or environment increases the conductivity of the electrolyte solution, creating conditions for electrochemical corrosion to occur.
- Electrochemical factors: The difference in potential between areas on the busbar surface forms small electrochemical cells, causing local currents and accelerating the corrosion rate.
3. Forms of busbar corrosion
Depending on environmental conditions and the nature of the material, busbar corrosion can occur in many different forms:
- Uniform corrosion: The entire busbar surface is corroded evenly, gradually reducing the cross-section of the busbar.
- Local corrosion: Only a part of the busbar surface is corroded, often appearing in locations with scratches, cracks or impurities attached.
- Cracking corrosion: Corrosion is concentrated on cracks or fissures on the busbar surface, causing the cracks to become wider and causing serious problems.
4. Consequences of busbar corrosion
Busbar corrosion causes many serious consequences, affecting the operation of the electrical system:
- Reducing the cross-section of the busbar: Reducing the conduction capacity of the busbar, causing local heating and increasing energy loss.
- Increasing resistance: Causing voltage drop on the busbar, affecting the quality of power supplied to the equipment.
- Causing electrical incidents: Short circuit, short circuit due to destruction of the insulation layer or contact between corroded metal elements.
- Reducing the life of the equipment: Corrosion reduces the mechanical strength of the busbar, easily leading to other damage and reducing the life of the entire electrical system.
5. Busbar protection methods
To prevent and minimize busbar corrosion, the following protective measures should be applied:
Surface protection
- Coating: Use specialized paints that are anti-corrosion, insulating and heat-resistant.
- Plating: Plating another layer of metal onto the busbar surface to form a protective layer, such as zinc plating, chrome plating.
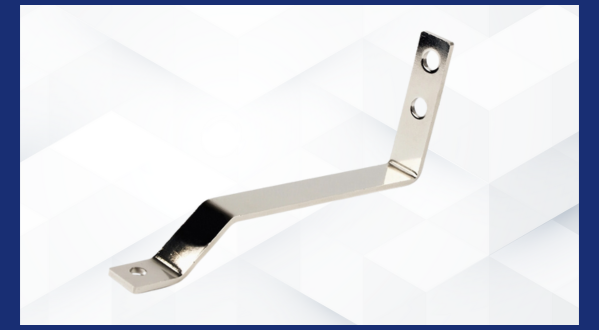
- Plastic pressing: Pressing a layer of plastic onto the busbar surface to form an insulating and protective layer.
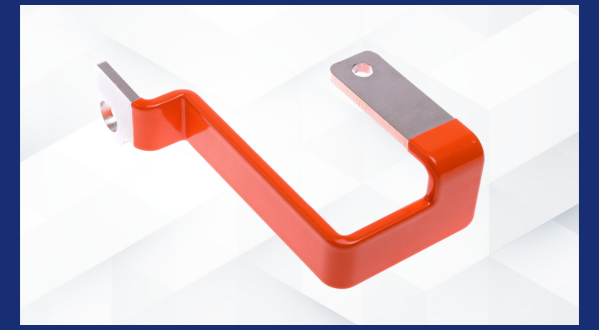
Environmental protection
- Keep the environment around the busbar clean and dry: Regularly clean, remove dirt and pollutants.
- Limit the penetration of corrosive substances: Use insulating, moisture-proof materials to cover the busbar.
Electrochemical protection
- Use sacrificial electrodes: Connect a metal with a stronger reducing property to the busbar, this metal will corrode instead of the busbar.
- Voltage regulation: Minimizes the voltage difference between points on the busbar to reduce corrosion current.
6. Measures for checking and maintaining busbars
To ensure stable operation of busbars and prolong their service life, it is necessary to carry out periodic inspection and maintenance measures:
- Periodic inspection: Check the busbar surface, joints, and contact points to detect signs of corrosion and damage.
- Timely repair: Repair or replace damaged parts to prevent corrosion from spreading.
- Cleaning: Periodically clean to remove dirt and contaminants on the busbar surface.
7. Conclusion
Busbar corrosion is a serious problem that affects the performance and reliability of the electrical system. Protecting busbars from corrosion is a mandatory requirement to ensure the safety and stable operation of the system.
To effectively protect busbars, it is necessary to combine many different measures, from choosing suitable materials, reasonable system design to periodic maintenance and inspection. Investing in busbar protection will help reduce repair and replacement costs and extend the life of the electrical system.